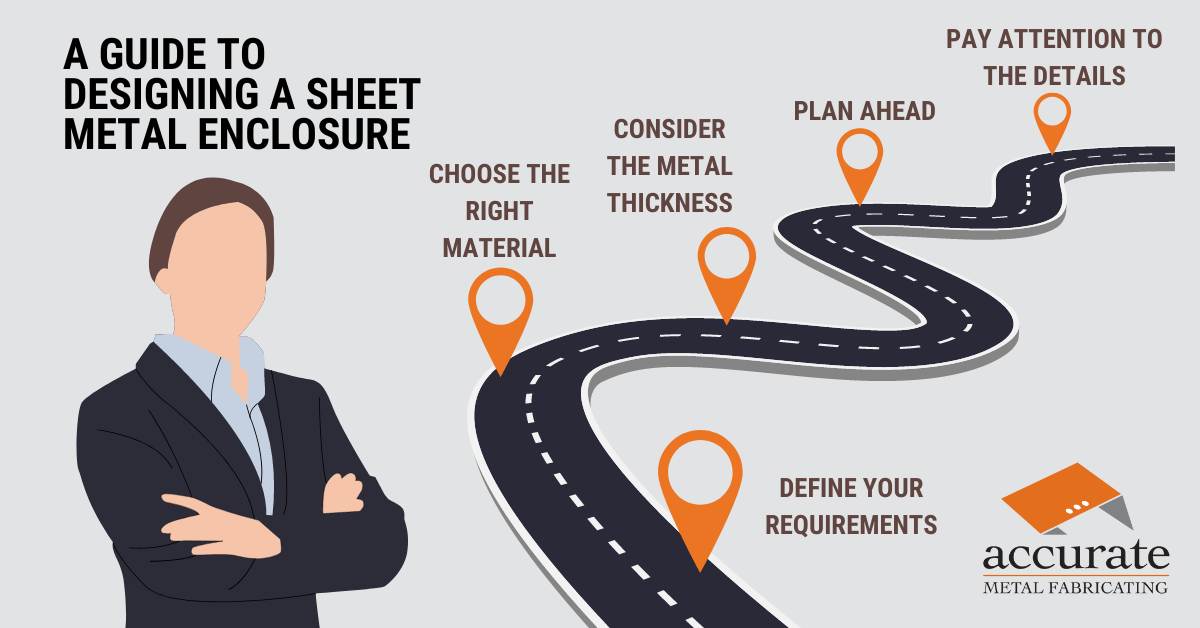
Designing a sheet metal enclosure requires careful consideration of various factors, including material selection, enclosure size, and, in some cases, design elements. Understanding these elements is essential to creating a functional and efficient protective housing that works for your specific use case. This guide will delve into the steps in designing a sheet metal enclosure to ensure that the final product meets your requirements.
What is a Sheet Metal Enclosure?
Before diving into the guide, we should define a sheet metal enclosure. A sheet metal enclosure, at its core, is a box with the specific intent to house something. This includes electrical junction boxes, touch screens (for a parking garage kiosk), and something as simple as a lock box to hold keys. These items are made from metal – specifically, sheet metal - formed through fabricating equipment such as press brakes. Before it is assembled and packaged, it is often powder-coated to a customer’s paint specifications. Now that we have defined a sheet metal enclosure let’s jump back into the guide and start the design process.
Step 1: Define Your Requirements
Before delving into the design process, clearly outlining the purpose and requirements of the sheet metal enclosure will help you stay on through the manufacturing process. As we examined above, these enclosures lend themselves to many applications. Determining the dimensions, shape, and specific equipment you need to house will help to guide a metal fabricator on what it will take to make what you need. Other requirements include your environmental conditions (will the enclosure be exposed to extreme temperatures, humidity, or chemical exposure). These considerations will help guide your metal fabricator in selecting the proper substrate for the application and advise on any design decisions you may require.
Step 2: Choose the Right Material For Your Sheet Metal Enclosure
Selecting the appropriate material for your sheet metal enclosure is crucial. Common materials used include:
Steel: Provides excellent strength and durability, making it ideal for rugged applications and industrial environments. If your enclosure will stay indoors, this might be the right option for you. Steel is an excellent medium for painting – the powder from the powder coating processes adheres nicely to the surface and can give a look that stands out. Think of something like a first aid kit. You often see these kits painted red as an easy visual indicator of a box that could quickly help with a scraped knee or aspirin for a headache. However, if your sheet metal enclosure stays outside for any time, steel is likely not a good choice for your enclosure. Mild carbon steel will flash rust when exposed to water. Although painting will prolong the process, it offers no rust protection if placed in an environment that is outside any facility.
Aluminum: High strength-to-weight ratio and corrosion-resistant, aluminum is often suitable for electronics and other portable sheet metal boxes. Because it is corrosion-resistant, it can stay outside for prolonged periods, making it an ideal choice for an application such as a lock box at a traffic guard. And because aluminum has a high strength-to-weight ratio, you can design a lighter box with the same physical properties as a sheet metal enclosure made from steel. But, that corrosion resistance and strength-to-weight ratio comes at a price. Aluminum is often double or more than the price of mild carbon steel.
Stainless Steel: Everyone loves how stainless steel looks – especially when you see it as a sheet metal box. The classic, iconic looks fit into almost any environment you can imagine – such as a hand dryer in a bathroom or an exposed metal junction box. The classic stainless steel look is typically one that you do not want to cover up. But powder coating is an option. Sheet metal enclosures made from stainless steel offer superior corrosion resistance, making it ideal for outdoor and harsh environments. Like aluminum, stainless comes at a 4x – 5x price more than carbon steel. And because it’s steel (and still has carbon), you will not get the weight-saving benefits you do from aluminum.
Each material has its advantages and disadvantages. Your choice will depend on factors such as budget, application, and required level of protection. A metal fabrication shop can walk you through the material options you can consider when you work with them early on during the engineering and prototyping phases.
Step 3: Consider Sheet Metal Thickness
The thickness of the enclosure's sheet metal affects its strength and rigidity. Thicker materials may offer better protection and durability but will increase the overall weight. The thicker the material you use, the heavier your sheet metal enclosure will be. Conversely, thinner materials are lighter but may not meet the intended application. Balance your needs to determine the optimal sheet metal thickness for your specific application.
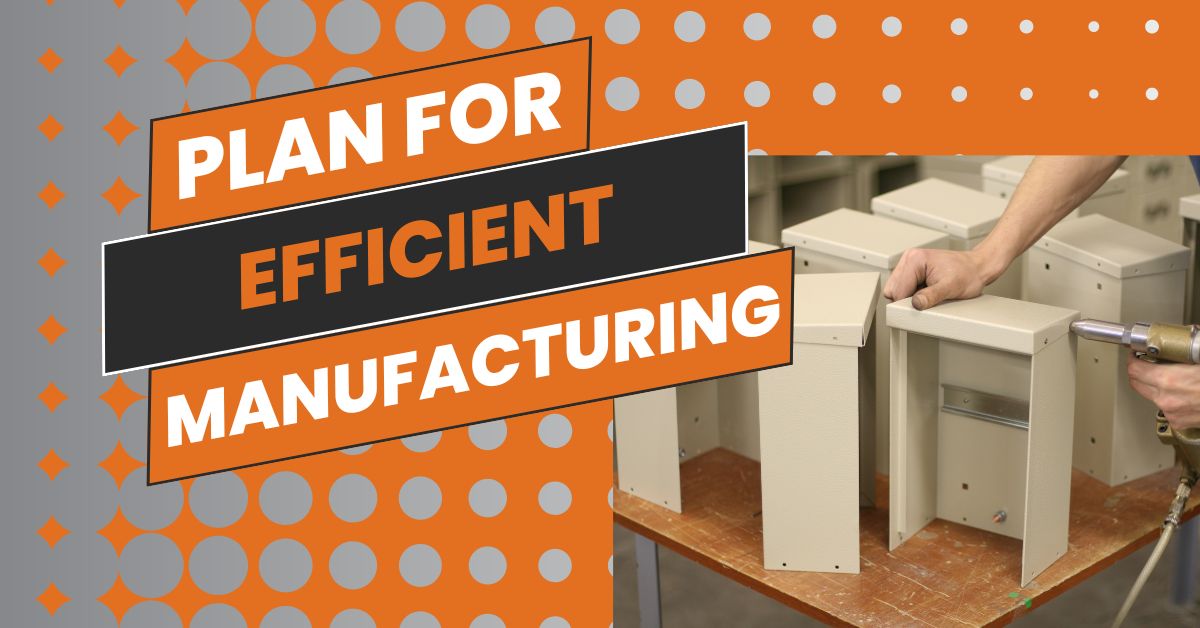
Step 4: Plan for The Manufacturing Processes
Sheet metal enclosures are fabricated in sheet metal fabrication centers such as Accurate Metal Fab’s location in Cicero, IL. These fabricators use many machines to process the metal to your specific standards. Stations such as laser cutting, press brake, robotic welding, and stamping could be used to manufacture a metal enclosure. During the design phase, your project managers will work with engineering to determine the manufacturability of your enclosure. They may make suggestions during the design process, such as avoiding complex shapes to limit any increase in production costs or lead time, including assembly difficulties. It will keep your costs down when you emphasize simplicity and efficient use of materials in a sheet metal box design.
Step 5: Incorporate Structural Features
Add appropriate features to reinforce the structural integrity of your sheet metal enclosure. Ribbing, flanges, and gussets are excellent ways to enhance strength without adding excessive weight. Additionally, consider including mounting brackets or rails for secure installation and ease of maintenance if your application will benefit from those features.
Step 6: Provide Ventilation and Thermal Management
Ventilation is essential for enclosures housing heat-generating equipment to prevent overheating. Incorporating vents, cooling fans, or perforated metal into your design will allow for proper air circulation so your internals do not overheat. Thermal management techniques such as heat sinks or conductive materials should also be considered to dissipate heat and ensure optimal performance efficiently.
Step 7: Pay Attention to Sealing and Gasketing
If your cabinet needs to be dust, water, or air-tight, ensure the proper sealing and gasketing so that nothing leaks in (or out). Rubber gaskets or silicone seals can prevent environmental contaminants from entering the enclosure, safeguard sensitive equipment, and ensure reliability. Vital welding techniques or POP riveting keep everything tight to ensure your new enclosure doesn’t break under pressure.
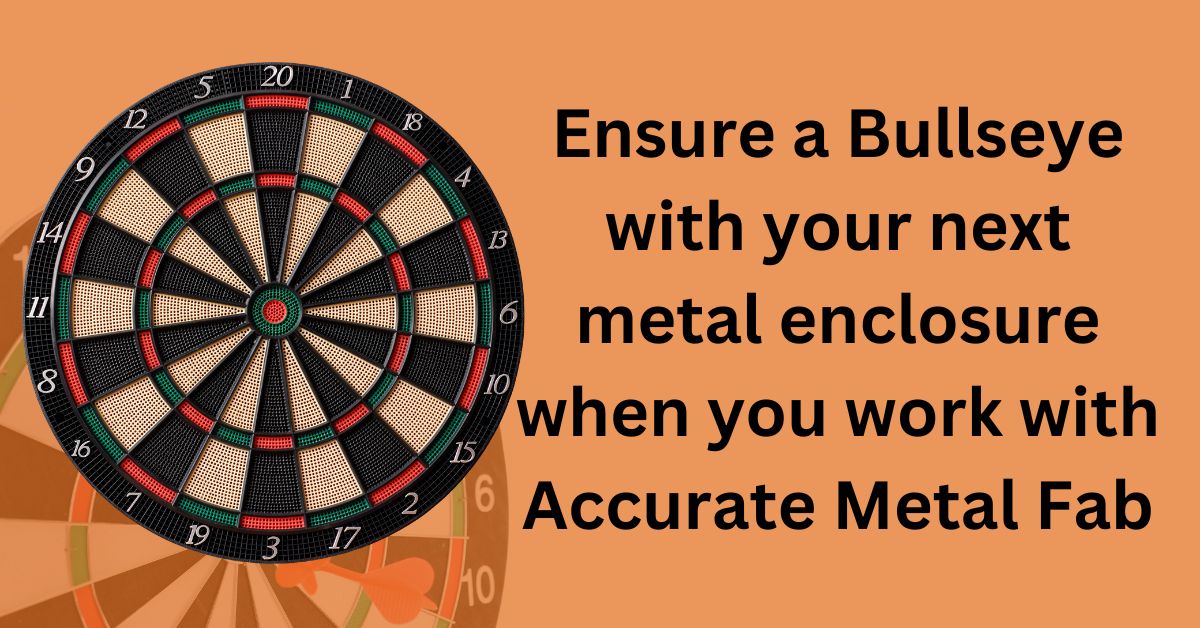
Accurate Metal Fab Is Your Go-To Source For Sheet Metal Enclosures
Designing a sheet metal enclosure requires a systematic approach, carefully examining material selection, size, structural elements, and functional requirements. Following the steps outlined in this guide, you can create a robust and effective enclosure that protects your equipment and enhances its performance. Accurate Metal Fabricating has a team of project managers and engineers who can guide your metal enclosure project from start to finish. Within our 140,000+ square foot facility, we have the sheet metal fabrication services you need to ensure your enclosure is crafted to perfection and meets your unique specifications. With the right design and fabrication, your sheet metal enclosure will serve as a durable and reliable housing for your valuable equipment. Reach out to us for more information.