When it needs to be done right...and right now.
As a POP display manufacturer since 1939, Accurate Metal Fabricating understands the industry's needs and delivers fast quotes and prototypes along with exacting manufacturing and assembly. However, their capabilities were tested when a California design firm called when their overseas fabricator dropped the ball in the 11th hour.
Developed by a California design firm, the POP display for a portable water purifying system blended science and nature with wood panels accenting the powder-coated and screened metallic frame. Signage needed to be affixed inside a blue-hued plastic holder and a security cord fastened to the base. It was designed to be located on a counter or stand, so the display must be light and feature a compact footprint. The displays would also have to be completed and shipped in time for the product launch, which was only two months away.
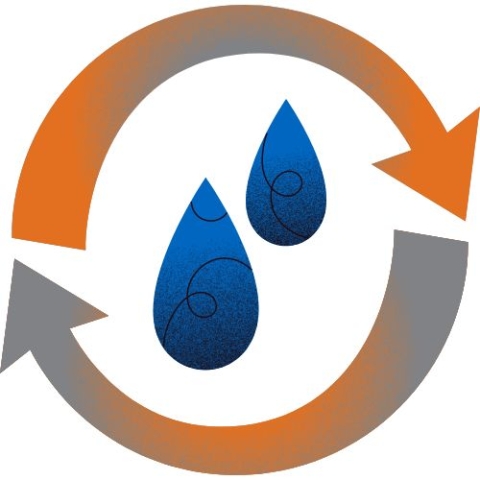
An overseas fabricator won the bid and was assigned to develop a display prototype. When the finished prototype was finally delivered, it lacked the style and look of the initial design. Because the fabricator could not weld the aluminum backer to the steel cradle as specified in the original design, they switched the material for the backer piece from aluminum to steel. This meant the loss of the brushed metal finish that gave the display its finished, upscale appearance. After receiving the prototype, it was clear that the overseas fabricator could not complete the job as designed. The design firm had to start from scratch with the product launch date approaching.
The project management team at AMF came calling at just the right time. After contacting the design firm as a follow-up to a mass mailing, they decided to give AMF a chance and sent the specs for them to begin fabricating a new prototype. AMF's expert engineering team quickly discovered why the overseas manufacturer had modified the materials - there was no way the piece could actually be built the way it was designed; the product cradle and the backer could not be welded together correctly. The cradle needed to be redesigned to attach the product cradle to the backer.
The AMF team quickly engineered a new design for the cradle that allowed the two pieces to be mounted together properly, featuring a uniform brushed aluminum finish. Within a week of getting the original specs, AMF approved the prototype. The design firm immediately assigned the job to AMF, who produced, assembled, and shipped 3000 units in time for the product launch. AMF's quick, proactive, and precise work saved the day. As a result, the design firm has since referred over 25 projects to AMF and continues to be yet another valued client.
-
A California design firm encountered issues with an overseas fabricator in the final stages of a project.
-
The initial overseas prototype failed to meet the design specifications, compromising the display's upscale appearance
-
The overseas fabricator's inability to weld aluminum to steel led to the use of incorrect materials
-
Within a week, AMF approved a new prototype that met the original design specifications
-
AMF successfully produced, assembled, and shipped 3,000 units in time for the product launch