Accurate Was Featured In The Fabricator
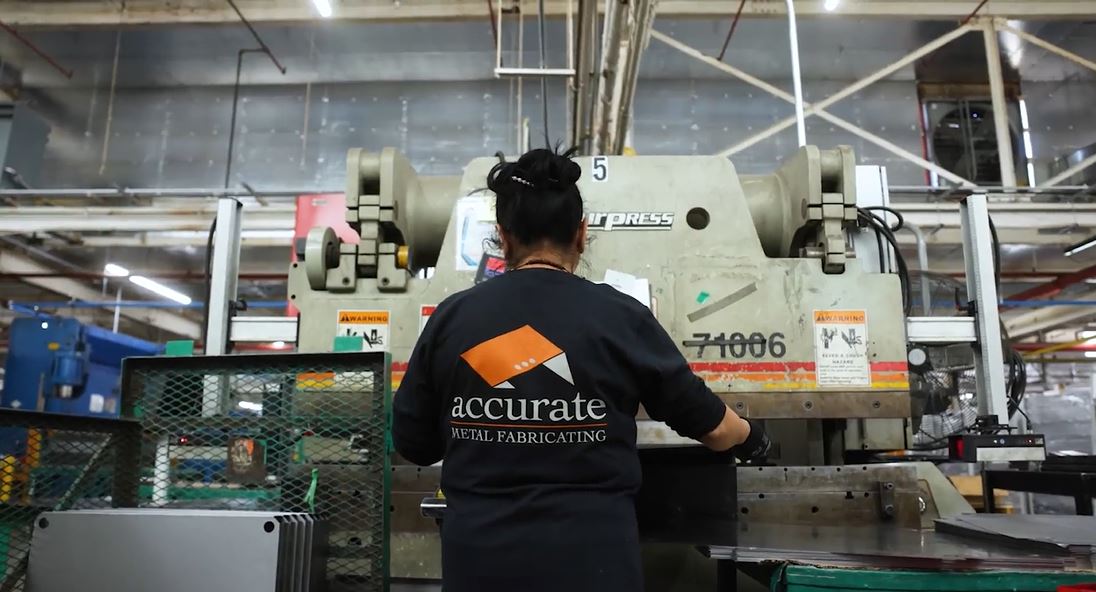
Reprinted and Modified From The Fabricator
Accurate Perforating doesn't just make holes anymore. It provides entire perforated and fabricated sheet metal components. The 200-employee Chicago manufacturer has done much to stand out in a consolidated sector.
The perforating industry once consisted of numerous small players clustered around Chicagoland and Pennsylvania. The shops were initially founded to serve the agricultural equipment needs and (especially in Pennsylvania) mining sectors. But over decades, the business changed. The perforation process itself had become viewed as a commodity service, and that, in turn, led to consolidation. Today, only a handful of prominent players remain, and one of them is Accurate Perforating (AP), a 200-employee operation based in Chicago.
But about a decade ago, AP started to follow a new path. Managers wanted the company to produce more than just the perforated sheet. They tried to fabricate and assemble that sheet into something larger and more complex.
Today, the company is no longer just about making holes; it's about making components that OEMs can place easily into their final assemblies and contractors can quickly install onto buildings. That's far different from what the company was right decades ago when a scrap peddler named Ralph Cohen fell in love with perforating—not for the hole-filled sheets the process produced, but what those sheets left behind.
FOR LOVE OF THE SLUGS
Before launching APC in 1942, Cohen had no intentions of becoming a perforator. He reveled in the deal—buying scrap low and selling it high—and some of his largest sources for scrap happened to be the perforation houses around Chicago.
"He was always a peddler at heart, and he became fascinated with his perforating clients because of the amount of scrap they generated," said Aaron Kamins, Cohen's grandson (on his mother's side). "He fell in love with the byproduct—the slugs that he would get from the perforators, and he said, 'You know, I could develop those slugs myself.' So he put in his first machine to generate those slugs."
During the early years, the perforation work complemented Cohen's primary scrap business, but over the years, this gradually shifted more toward perforation. APC moved into its facility in 1952 and remained a small enterprise for decades. Then, in 1982, managers jumped on an opportunity to purchase Standard Perforating, a competitor just a few miles away that had just undergone a labor dispute with its union and was struggling financially. APC moved Standard Perforating's employees and machines over to its facility. "That doubled the size of the business overnight," Kamins said, adding that in 2002, APC purchased another Chicago-based perf house, Semrow Perforated Products.
FOOTHOLD IN FABRICATION
For decades, APC has performed shearing—and it's not an everyday shearing process, either. Some shearing occurs automatically in a separate station, connected to the press control, as the sheets emerge from the die.
Specific jobs, such as one in which each panel is a different size, each with an unperforated margin around the edge, require a secondary shearing process. A technician places pins in the last row of perforations, which stick up and allow the shearing operator to gauge off the edge of the perforation (the critical dimension) and not the edge of the blank.
Besides shearing, though, the company's fabrication offering in the 1990s was a little extensive, and it certainly didn't include comprehensive assembly or welding services. Between 2000 and 2005, Mike Beck, Vice President of Sales and Engineering, helped bring in machines to expand APC's capabilities. "Our existing customer base's demand for fabrication was growing," he said.
Then, in early 2005, came a phone call that accelerated the company's push into fabrication. It was a contractor for the new American Airlines World Gateway terminal at JFK, and he had a problem. The new concourse had thousands of perforated ceiling panels. The perforations weren't unusual—0.125-inch-diameter holes punched in 0.050-inch-thick aluminum; the holes' staggered orientation (lining up horizontally but not vertically) aided noise reduction and airflow.
Fit-up between the panels was critical, and this was what the contractor called about. Thousands of panels had arrived at the site, perforated and with edges flanged, but when they were installed, some bowed slightly. Many panels had dimensions different from what they should have been, which wreaked havoc on fit-up. On top of all this, many panels arrived at the site severely damaged.
The contractor sprung the question: Could APC provide dimensionally accurate perforated panels? One more thing—the grand opening is just 90 days away.
APC dove into the job, manufacturing 17,000 panels with acoustic backing material and the proper perf patterns that ensured noise reduction and proper airflow. It worked with a corrugated box manufacturer on the packaging so the panels would arrive at JFK without a scratch.
Most significant, at least regarding the company's evolution, was APC's work with Advanced Display, a precision sheet metal fabricator in Chicago. At the time, the fabricator focused on the point of purchase (POP) display industry (hence the fabricator's name) but contracted with different companies as well, including APC.
Advanced Display had the precision press brakes and forming expertise this job required, plus the capacity to manufacture the panels within the short lead time required. The 2- by 5-foot perforated panels required a tight dimensional tolerance in length, width, and edge-flange depth.
Working together, APC and Advanced Display churned out 170,000 square feet of perforated panels, fabricating and painting them on time to be painted and installed before the grand opening in July 2005, when then-New York City Mayor Michael Bloomberg spoke below the space-age, dramatically white ceiling of the new Terminal 9.
HOLEMAKING ON THE LEVEL
Because the perforation press creates a large area of holes in one hit with one die, it tends to distribute forming stresses evenly, but the unequal stresses are still there, and this causes distortion. The plate that is 0.25 in. thick emerges from the perf press almost in a half-moon shape. It curls the entire sheet, but it curls it evenly.
By making hole-intensive patterns on the turret punch press, technicians can minimize stress by punching in different areas of the sheet, starting away from and moving toward the clamps. They use machine features that change the approach speed of the ram or use the stripper to hold the workpiece in place before the punch contacts the sheet surface. All this helps distribute the stress induced by the punching force. All the same, for many jobs, the distortion is, again, still there.
For this reason, the company sends all perforations and other hole-intensive jobs through one of seven high-powered Herr-Voss Stamco precision levelers, which equalize the stresses to produce a flat, perforated sheet. The levelers handle everything from 0.012- to 0.312-in. sheet (though thickness capability depends on material type). "We put a lot of stress into the material," Kamins said, "but we have a way of taking that stress out."
"It takes a thick, U-shaped plate, even stainless steel, that looks like we never could use it," Beck said. "We send it through our CNC levelers, and it comes out perfectly flat."
This has allowed the company to tackle hole-making work that couldn't be done without subsequent leveling. The leveling also makes the punched blanks consistently flat for downstream forming and assembly, especially for the component work that flows through Accurate Metal Fabricating.
QUANTITY CONSIDERATIONS
When it comes to making holes, it's hard to beat a perf press's productivity. "On each stroke, we can punch up to 1,600 holes," Kamins said. You can't do that using any other technology." "This is high-speed stamping," Beck said. "Our perf presses run at 300 strokes per minute."
Multiply this by the 18 perforating presses APC has on its floor, and you get a lot of hole-making capacity. With throughput like this, perforation presses thrive on high volumes. The CNC presses can perform skip feeds, leaving a section of the strip unperforated. Some tools can have block punches to make square or rectangular cutouts within a perf pattern. But for the most part, the process's sweet spot is consistent hole patterns.
High-volume hole-making goes to the perf presses; low-volume hole-making work goes to the turret punch presses—but what about the volumes in between? "For some applications, if we cluster-punched a job on a turret press, we wouldn't have enough time in the day," Beck said. "A job may call for 150 sheets, which would take about two hours on the turret press simply because of the number of holes. And we have just five turret presses."
BRANDING WITH HOLES
Many OEM and POP customers have approached AP about a way to design their brand logos into a perforated sheet. AP employed programmers experienced in hole-intensive jobs on the turret punch press, and programming logo shapes, while intricate, was relatively easy for them.
As Kamins recalled, "After we did this, several clients came to us with a picture and asked, 'Can you punch this?'" Kamins added that the request evolved into a service AP now calls Picture-Perf, in which the company punches holes in a pattern that creates a logo, graphic, or picture.
"We saw similar things done differently before," said Beck. "So we asked, 'What if we use different-sized holes with different open areas and spaces between those holes?'"
The pattern can be small, in the corner of one panel on a POP display, or cover a building facade. For the new apartment complex in downtown Chicago, APC is providing 51 panels, each five by 13 ft., that, when assembled, depict a giant picture of the Greek Parthenon.
PERF PRESS QDC
Years ago, every operator at Chicago-based Accurate Perforating changed out his press differently. Now, operators work under a standardized quick-die-change (QDC) process. Pit crews stage the tools before the previous run is finished and help the operator perform the changeover.
"We built tool cabinets so that all the tools needed for the operation sit right there," said Beck. "The operator no longer needs to walk two presses down and say, 'Hey! Johnny, I need a wrench.'"